In the competitive world of manufacturing, the mantra of continuous improvement (CI) resonates through the corridors of factories and the strategy meetings of managers. It’s not just a buzzword; it’s a mindset, a relentless pursuit of perfection, knowing full well it’s an ever-moving target. But what principles guide this journey? And in an era brimming with technological advancements, how do these timeless principles intertwine with modern tech to drive improvement? Let's dive into the principles of CI and the pivotal role technology plays.
The Seven Pillars of Continuous Improvement
Continuous improvement in manufacturing is built on several key principles that, when applied diligently, can transform operations from the inside out. Here’s a closer look:
- Kaizen: The heart of CI, Kaizen is about making small, incremental changes regularly. It champions the idea that everyone in the organization, from the CEO to the shop floor worker, has a role in improvement.
- Gemba: Gemba takes us to the "real place" where work happens. It emphasizes the importance of understanding the production floor and engaging with frontline workers to identify areas for improvement.
- Waste Elimination (Muda): Inspired by Lean manufacturing, this principle focuses on identifying and eliminating waste in all its forms—be it overproduction, waiting time, transportation, over-processing, inventory, motion, defects, or unused talent.
- Standardization: Consistency is key in CI. Standardizing processes ensures that improvements are maintained over time, and best practices are consistently applied across the board.
- Continuous Flow: By optimizing workflow, manufacturing aims to achieve a state where work moves smoothly without interruptions, leading to higher efficiency and productivity.
- Jidoka (Automation with a Human Touch): This principle is about automating processes in such a way that machines can detect and address quality issues autonomously, without sacrificing the human element of oversight and intervention.
- Root Cause Analysis: When problems arise, the goal is not just to address the symptoms but to dig deep and solve the underlying issues, ensuring they don't recur.
Principles of Continuous Improvement & Technology: A Powerful Duo
Incorporating technology into CI principles can amplify their impact, offering new ways to tackle old challenges. Let’s break down how:
- Kaizen & Tech: Digital tools and platforms facilitate easier collaboration and idea sharing, making the Kaizen process more inclusive and efficient. New continuous improvement tools like Avatour allow team members, regardless of location, to participate in improvement discussions, providing 360° views of processes and problems in real-time.
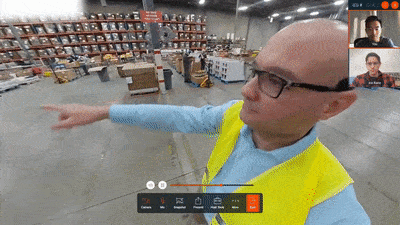
- Gemba Goes Digital: With technologies like Avatour, leaders can virtually visit the shop floor (“virtual Gemba”) to observe processes and engage with workers without the constraints of physical presence, making frequent "Gemba walks" a reality, even from miles away.
- Waste Elimination through Data: Advanced analytics and IoT devices offer real-time data on production processes, helping to pinpoint waste more accurately and swiftly. This data-driven approach to identifying Muda transforms decision-making from reactive to proactive.
- Standardization Meets Flexibility: Digital tools enable the documentation and dissemination of standardized processes while allowing for quick updates as improvements are made. This dynamic standardization ensures that teams always have access to the latest best practices.
- Enhancing Continuous Flow: Automation and simulation software help in designing and testing workflow changes virtually, minimizing disruptions and optimizing flow before changes are implemented on the shop floor.
- Jidoka in the Digital Age: Modern automation technologies are equipped with sensors and AI that not only detect defects but also learn over time, enhancing their ability to prevent quality issues autonomously.
- Root Cause Analysis with Advanced Analytics: Technologies like machine learning can analyze vast amounts of data to uncover patterns and predict potential failures before they happen, making root cause analysis more insightful.
Moving Ahead
The principles of continuous improvement provide a robust framework for manufacturing excellence, but it’s the integration with technology that truly propels these principles into the future. Platforms like Avatour are at the forefront of the new continuous improvement tools, offering new opportunities for collaboration, problem-solving, and efficiency enhancement. By embracing both the time-honored principles of CI and the innovative solutions technology offers, manufacturers can navigate the complexities of modern production with greater agility and success.
In this ever-evolving landscape, the commitment to continuous improvement, underpinned by both principle and innovation, is what sets apart the leaders from the followers. Whether you’re streamlining your supply chain, enhancing product quality, or cultivating a culture of perpetual progress, the journey of improvement is continuous, and every step forward counts.