Cultivating a Continuous Improvement Mindset in Manufacturing
In the fast-paced world of manufacturing, where efficiency and innovation are paramount, the cultivation of a continuous improvement (CI) mindset stands as a cornerstone of organizational culture. This mindset is not merely about adopting specific tools or methodologies; it’s about fostering an environment where every team member is engaged in the pursuit of betterment, constantly questioning the status quo and seeking out opportunities for enhancement. Let's delve into the essence of the continuous improvement mindset, its impact on manufacturing, and the role of technology in nurturing this culture.
Understanding the Continuous Improvement Mindset
A CI mindset is characterized by several key attributes: a relentless pursuit of perfection, an openness to change, and a commitment to learning. It's a mindset that views failures not as setbacks but as opportunities for learning and growth. This philosophy is deeply rooted in the principles of Kaizen, which emphasizes that small, ongoing positive changes can reap significant improvements.
The Impact of a CI Mindset
Research in organizational behavior consistently highlights the positive outcomes of a CI mindset. A study published in the Journal of Organizational Change Management points out that organizations embracing this mindset not only achieve higher operational efficiencies but also foster a more engaged and motivated workforce. Employees in such environments are more likely to contribute ideas, participate in problem-solving activities, and embrace new challenges with a positive attitude.
Strategies for Success
Developing a CI mindset within an organization requires deliberate effort and strategies. Here are some approaches that have proven effective:
- Leadership by Example: Leaders must embody the CI mindset, demonstrating a willingness to change and a commitment to personal and organizational growth.
- Employee Empowerment: Empowering employees to identify issues and propose solutions encourages ownership and engagement, essential components of the CI mindset.
- Education and Training: Ongoing education on CI principles and techniques, including Lean manufacturing and Six Sigma, equips employees with the tools they need to contribute effectively.
- Recognition and Rewards: Acknowledging and rewarding improvements and innovations reinforce the value placed on continuous improvement efforts.
Technology and the CI Mindset - Examples
In today’s digital age, technology plays a pivotal role in supporting and enhancing the CI mindset. Avatour exemplifies the new breed of continuous improvement tools. It enables lean managers to go beyond traditional video conferencing or static digital twins by providing immersive, real-time experiences that break down geographical barriers and enhance collaboration.
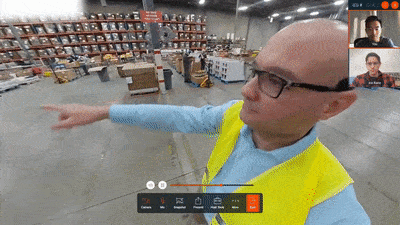
- Enhancing Visibility: Avatour allows team members, regardless of location, to gain a comprehensive understanding of operations, fostering a shared sense of purpose and collaboration.
- Facilitating Real-Time Feedback: The ability to collaborate and provide feedback in real time accelerates the improvement cycle, making it easier to implement and assess changes quickly.
- Supporting Education and Training: Avatour can be used as a tool for remote education and training, allowing employees to witness and learn from best practices across different locations, further embedding the CI mindset.
The Path Forward
The journey toward cultivating a CI mindset is ongoing and evolving. It's about creating a culture where improvement is not just encouraged but expected, where every employee feels empowered to contribute, and where technology like Avatour plays a crucial role in bringing these aspirations to life. As manufacturing continues to evolve, continuous improvement techniques and the adoption of innovative tools will remain central to achieving operational excellence and sustaining competitive advantage. In this landscape, the CI mindset is not just an advantage—it's a necessity.