If you're looking to improve efficiency and productivity in your business, you may have come across the term "gemba." Gemba is a Japanese term that translates to "the real place" or "the actual place." In a business context, gemba refers to the place where value is created, whether that's a factory floor, a sales office, or a customer service center. By going to the gemba, managers and employees can gain a better understanding of the work processes, identify opportunities for improvement, and make more informed decisions. Embracing the concept of gemba can lead to a more streamlined and effective operation, ultimately driving better results for your business.
When business decisions are made away from the job site or factory floor, leaders and managers may not be aware of the challenges and inefficiencies of the day-to-day. As a result, specific areas of the process that need attention and improvement are often overlooked.
Continuous improvement leaders at Toyota recognized this problem, and implemented the practice of going and seeing where the work happens, now referred to as a “Gemba Walk”. They recognized the importance of understanding real-world problems through first-hand observation to make more informed decisions to improve business processes.
While this practice started in the automotive industry, it’s now common practice across industries as part of the Lean management philosophy.
Let’s take a look at “Gemba” and “Gemba Walk” in more detail.
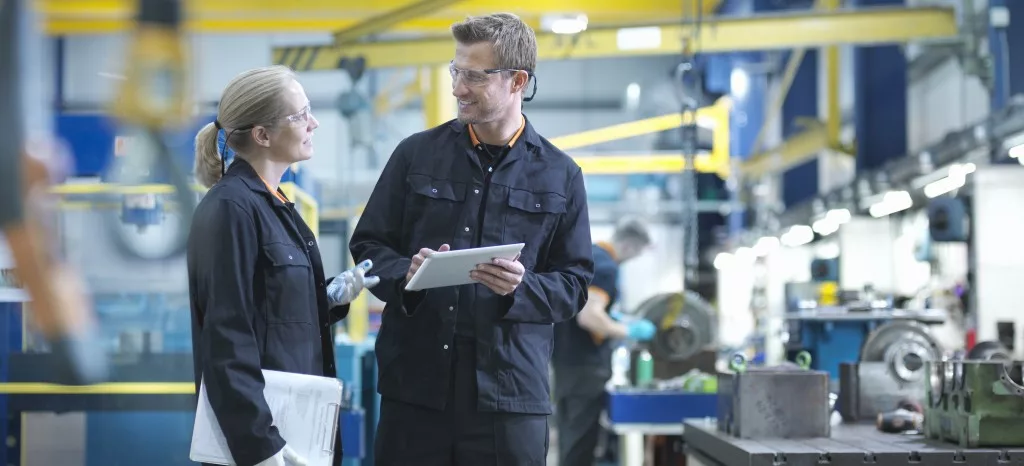
What is a Gemba?
Gemba (or sometimes written as Genba) is a Japanese term that translates to “the actual place”. In the context of business, Gemba refers to the place where work actually happens such as the shop floor or a job site.
The term is most commonly used in Lean Methodology and Six Sigma, to talk about sites and facilities where value creation occurs.
What is a Gemba Walk?
A Gemba Walk is a structured workplace walkthrough conducted to better understand operations on site and identify opportunities for improvement.
The practice of walking the Gemba was first introduced in the 1950s by Taiichi Ohno, the founder of the Toyota Production System, who stressed the importance of going to the place where the work is happening as part of the continuous improvement process.
A routine Gemba Walk involves following the value-stream from end-to-end, observing the work done at each stage. Typically, leaders will follow a single product family or manufacturing process from beginning to end, documenting and taking note of areas of inefficiency.
Check out our 10 essential tips to get the most out of your next Gemba walk.
Who Performs a Gemba Walk?
Gemba Walks are first and foremost, a way to optimize operational efficiency. Therefore, individuals who are responsible for implementing, enforcing, and improving operational practices should perform Gemba Walks.
This responsibility should not be limited to direct managers but be extended to all levels of management across various functions and departments.
In performing a Gemba Walk, each individual will observe things differently according to their expertise. The more input you gather, the more context you have into understanding the process and uncovering what is adding versus subtracting value.
Key Benefits of Gemba Walks
Remember, the purpose of a Gemba Walk is to observe and learn about the processes on site. Here are a few of the key benefits:
- Reliable insights through first-hand observations
Leaders who regularly walk their sites see beyond data and outcomes, and gain insights into day-to-day operations. Having a deep understanding of these processes can help identify bottlenecks and areas of inefficiency that might otherwise remain undetected.
- Gain a holistic view of the operation
Through observing various aspects of the value-creation process, leaders can build a more holistic view of the operations. This helps to better understand how each component of the business impacts another, which drives quality of service, product, and customer satisfaction.
- Understand people and processes equally
Interacting with employees is a crucial part of a successful Gemba Walk. Not only do leaders get the rare chance to engage directly with teams on-site, but their input is crucial to having a deeper understanding of what’s working and not working in the day-to-day.
Challenges of Gemba Walks
Common pitfalls of Gemba Walks typically result not in their foundational purpose, but how they are executed and by whom.
- Losing sight of purpose: process observation, not performance evaluation
Gemba Walks are meant to be used as a mutual empowerment and optimization tool. Those performing the walk must walk a fine line between wanting to observe and learn versus making workers feel like they are being judged and audited. Communicate the purpose of the walk clearly: process observation, not performance evaluation.
- Urge to implement change during the walk
While walking the floor, managers and leaders may feel inclined to share their opinions on the spot. This is not an effective way to implement change, and should be avoided as much as possible. Remember to have a plan to share ideas and findings after the walk to then strategize on how to implement the necessary changes moving forward.
- Geographical and logistical challenges
Coordinating travel and lodging for multiple team members can be incredibly time consuming and costly. Oftentimes, those who would benefit the most from walking the floor are too busy to spend days on the road. Ideally, Gemba Walks are conducted frequently to maintain consistent visibility of what’s happening on site. As a result, many Lean leaders have started to use remote collaboration technology to enable more frequent access of distant sites.
Predictions for Gemba Walks
Process optimization will be more important than ever in 2023 and we anticipate Gemba walks will become more common. But as the cost of travel increases and willingness to travel decreases, companies will need to find new ways to gain visibility of their operations on site.
One clear avenue for improvement will be the use of emerging technologies to implement Virtual Gemba Walks. With the right technology, remote teams perform walkthroughs virtually without sacrificing the quality of observation and collaboration.
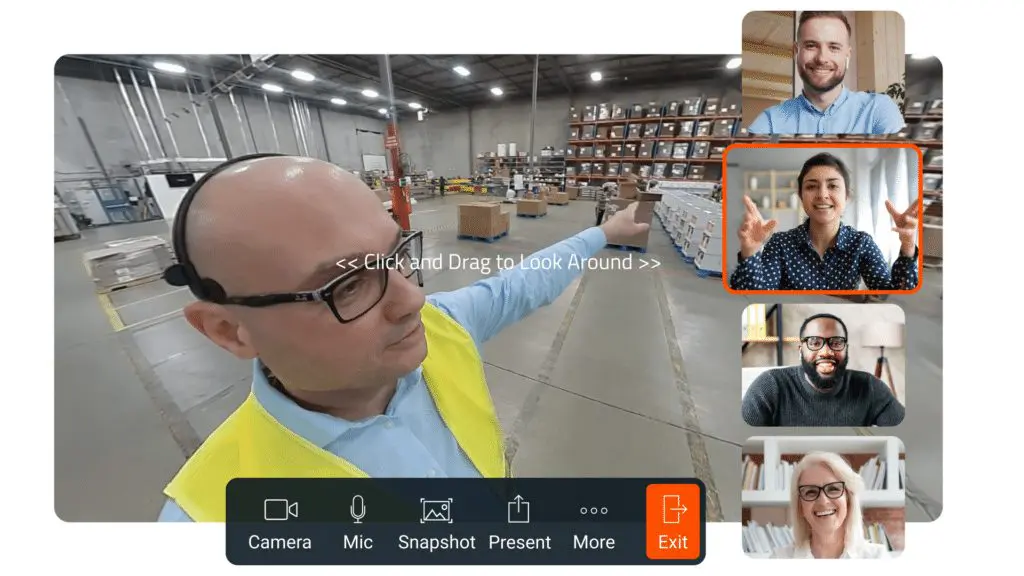
Avatour delivers the most effective way to walk the Gemba virtually.
The Avatour platform creates a shared feeling of presence in a physical location using real-time communication and 360° video capture.
Whether you manage one location or 100, Avatour provides in-person visibility without the hassle of travel so you can focus on what’s important: the Gemba.
Click to learn more about the Avatour platform.