In today's fast-paced manufacturing industry, ensuring the safety of employees and the overall work environment is of utmost importance. A safety audit is a comprehensive assessment that allows manufacturers to identify potential hazards and implement control measures to mitigate risks. This article will delve into the significance of safety audits in a manufacturing setting, discuss the key benefits they offer, highlight the essential elements of a manufacturing safety audit checklist, outline the steps to conduct an effective safety audit, and shed light on common mistakes to avoid. By following this ultimate manufacturing safety audit checklist, companies can create a safer work environment and protect the well-being of their employees.
Understanding the Importance of a Safety Audit
A safety audit is an essential tool that helps manufacturers proactively identify and manage potential safety hazards. With the aim of preventing accidents, injuries, and ensuring compliance with safety regulations, conducting regular safety audits is crucial. These audits provide insights into the gaps and shortcomings in an organization's safety protocols, allowing for necessary improvements to be made to protect employees and minimize production downtime.
The Role of Safety Audits in Manufacturing
In a manufacturing environment, where equipment, machinery, and hazardous substances are often present, safety audits play a vital role in safeguarding the well-being of employees. By evaluating safety practices and processes, audits help manufacturers identify areas that need improvement, such as equipment maintenance, employee training, and emergency preparedness. This proactive approach helps identify potential risks and prevents accidents, ensuring a safe work environment for all.
For example, during a safety audit in a manufacturing facility, the auditor may observe that some employees are not wearing the appropriate personal protective equipment (PPE) while working with hazardous substances. This finding highlights the need for additional training and reinforcement of safety protocols to ensure that all employees are aware of the importance of wearing PPE and are equipped with the necessary gear to protect themselves.
In addition to identifying areas for improvement, safety audits also provide an opportunity for manufacturers to recognize and acknowledge employees who consistently adhere to safety protocols. By publicly recognizing their efforts, manufacturers can foster a culture of safety and encourage others to prioritize safety in their daily work activities.
Key Benefits of Regular Safety Audits
Regular safety audits offer numerous benefits to manufacturers. First and foremost, audits help identify workplace hazards and potential risks, enabling companies to implement control measures that reduce the likelihood of accidents. By creating a safer work environment, manufacturers can minimize injuries and their associated costs, such as medical expenses and worker compensation claims. Safety audits also ensure compliance with industry regulations, avoiding penalties and legal issues.
Moreover, demonstrating a commitment to maintaining high safety standards enhances the reputation of manufacturers, attracting skilled employees and building trust among stakeholders. When potential employees see that a manufacturing company prioritizes safety and invests in regular audits, they are more likely to view the organization as a desirable place to work. Similarly, customers and business partners are more inclined to engage with manufacturers who prioritize safety, as it demonstrates a commitment to quality and responsible business practices.
In conclusion, safety audits are a critical component of maintaining a safe and productive manufacturing environment. By conducting regular audits, manufacturers can identify areas for improvement, reduce the risk of accidents, and ensure compliance with safety regulations. Furthermore, the benefits of safety audits extend beyond the workplace, as they contribute to the overall reputation and success of manufacturers in the industry.
Essential Elements of a Manufacturing Safety Audit Checklist
A thorough manufacturing safety audit checklist should encompass various critical elements that contribute to safety in the workplace. By assessing these elements, manufacturers can identify areas that need improvement and take appropriate actions to mitigate risks.
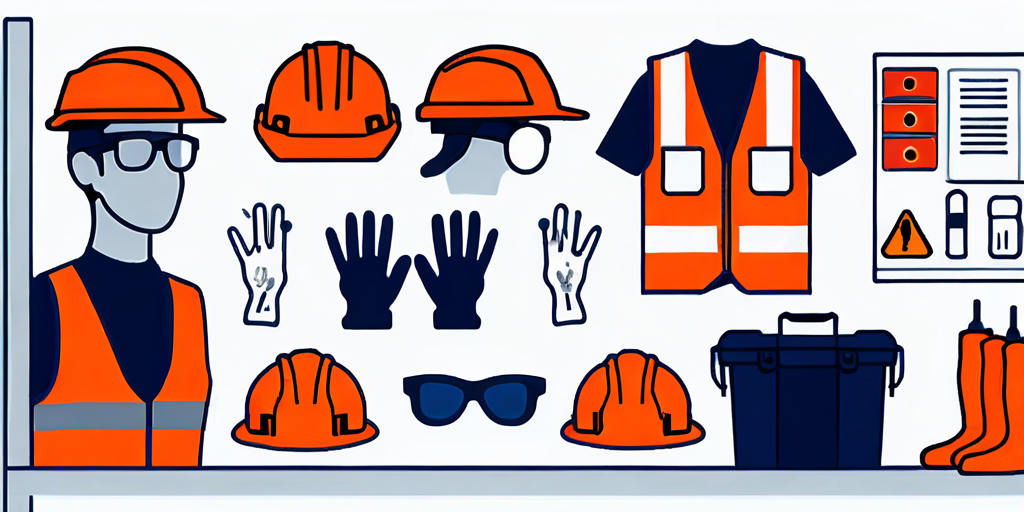
Safety Equipment Inspection
The first element of a manufacturing safety audit checklist is to conduct a comprehensive inspection of safety equipment. This includes assessing the functionality and maintenance of fire extinguishers, emergency alarms, personal protective equipment (PPE), safety harnesses, and other safety tools. Regular inspections and prompt repairs or replacements ensure that employees have easy access to functioning safety equipment when needed.
Hazard Identification and Control Measures
Hazard identification and control measures are crucial for maintaining a safe working environment. A manufacturing safety audit should involve identifying potential hazards, such as exposed wires, slippery floors, or malfunctioning machinery, and implementing control measures to mitigate risks. This may include labeling hazardous areas, improving signage, and ensuring proper equipment maintenance practices.
Employee Training and Awareness
Employees' knowledge and awareness of safety procedures significantly impact the overall safety culture within an organization. A manufacturing safety audit checklist should assess the effectiveness of employee training programs and their understanding of safety protocols. Regular refresher training sessions and clear communication channels for reporting safety concerns should be established.
Steps to Conduct an Effective Safety Audit
Conducting an effective safety audit requires careful planning, meticulous execution, and thorough follow-up. By following a structured approach, manufacturers can maximize the benefits of their safety audits and continuously improve their safety practices.
Pre-Audit Preparation
Prior to conducting a safety audit, manufacturers should ensure that they have a detailed checklist in place. The checklist should cover all essential elements, as mentioned previously, and provide a clear framework for evaluating safety practices and protocols. It is also essential to communicate the audit plan to employees, fostering a collaborative approach and encouraging their active participation.
During the Audit: What to Look For
During the safety audit, it is crucial to pay close attention to various aspects of the manufacturing facility. Inspect the workplace for any potential hazards, evaluate the condition of safety equipment, and assess employees' adherence to safety protocols. Engage in conversations with employees to gather their insights and feedback on safety practices. Note any deviations from established safety standards and identify areas for improvement.
Post-Audit: Review and Improvement
After completing the safety audit, it is essential to review the findings and develop an action plan to address the identified gaps. This plan should prioritize immediate concerns and establish clear timelines for implementing corrective measures. Regular follow-up audits should be conducted to monitor progress and ensure the sustained effectiveness of safety protocols.
Common Mistakes to Avoid in Safety Audits
While safety audits are crucial for maintaining a safe work environment, certain mistakes can undermine their effectiveness and hinder progress. Avoiding these common mistakes is essential to derive maximum benefit from safety audits.
Inadequate Planning
One of the pitfalls in safety audits is inadequate planning. Manufacturers should allocate sufficient time and resources to prepare a comprehensive audit checklist and communicate the audit schedule to all relevant stakeholders. Proper planning ensures that the audit covers all critical areas and provides meaningful insights.
Overlooking Minor Safety Issues
Another mistake to avoid is overlooking minor safety issues. While major hazards may draw immediate attention, overlooking minor concerns can lead to more significant problems over time. Manufacturers should ensure that even minor safety issues, such as loose handrails or damaged floor tiles, are promptly addressed to create a truly safe working environment.
Neglecting Employee Feedback
Employees are an invaluable resource when it comes to identifying safety hazards. Neglecting their feedback and suggestions undermines the overall effectiveness of safety audits. Manufacturers should actively encourage employees to share their safety concerns and always consider their insights when developing strategies to improve safety practices.
Conclusion
Safety audits are an indispensable tool for manufacturers striving to create a safe work environment and prioritize the well-being of their employees. By understanding the importance of safety audits, recognizing their key benefits, and following a comprehensive manufacturing safety audit checklist, companies can minimize risks, comply with regulations, and enhance their reputation. Conducting regular safety audits, avoiding common mistakes, and continuously improving safety practices ensure the long-term success and sustainability of manufacturing operations while safeguarding the most critical asset - the workforce.

Enhance Your Safety Audits with Avatour
As you prioritize the safety and well-being of your workforce, consider the cutting-edge capabilities of Avatour to elevate your manufacturing safety audits. Our platform revolutionizes the way you conduct inspections, tours, and training by offering live and recorded 360° capture and collaboration. Experience full 360° visibility during your safety audits, enabling remote collaborators to immerse themselves in your facility's environment in real-time, without the need for physical travel. Embrace a more efficient, productive, and environmentally friendly approach to safety management. Learn more about Avatour and discover how it can transform your safety audit processes.