Lean Manufacturing Best Practices: A Gateway to Operational Excellence
In the world of manufacturing, efficiency and continuous improvement aren't just goals—they're necessities for survival and success. Lean manufacturing, with its roots deeply embedded in the Toyota Production System, offers a blueprint for operational excellence. This guide serves as an introduction to some of the most widely recognized best practices in lean manufacturing, shedding light on the pathways companies can take towards becoming more efficient, agile, and customer-focused.
Embrace the 5S Framework
One of the foundational elements of lean manufacturing is the 5S framework: Sort, Set in order, Shine, Standardize, and Sustain. This methodology helps create a clean, organized, and efficient work environment conducive to productivity.
- Toyota, the progenitor of lean manufacturing, has famously applied the 5S principles to eliminate waste, improve processes, and increase productivity. This disciplined approach to workplace organization has seen Toyota consistently rank as a leader in manufacturing efficiency and quality.
Implement Continuous Improvement (Kaizen)
Kaizen, or continuous improvement, is the practice of constantly seeking ways to improve operations and reduce waste. It involves every employee, from executives to floor workers, in the process of finding and implementing small, incremental changes that add up to significant improvements over time.
- General Electric saw remarkable results from implementing Kaizen. By engaging all employees in continuous improvement efforts, GE reported a 75% reduction in manufacturing cycle times and significant improvements in product quality and customer satisfaction.
Utilize Value Stream Mapping
Value stream mapping is a lean tool that helps visualize and understand the flow of materials and information as a product makes its way through the value stream. It identifies bottlenecks and waste, providing a clear roadmap for improvement.
- Nike utilized value stream mapping to re-engineer its supply chain, resulting in a 30% reduction in lead times and a significant decrease in production costs. This not only improved efficiency but also increased Nike’s ability to respond to market changes.
Foster a Culture of Empowerment and Engagement
Lean manufacturing thrives in environments where there is a strong culture of empowerment and engagement. When team members at all levels are encouraged to contribute ideas and take ownership of processes, the results can be transformative.
- Intel has cultivated a culture where lean principles flourish, encouraging employee participation in problem-solving and improvement initiatives. This culture of empowerment has led to innovative solutions that have streamlined operations and reduced costs.
Apply Just-In-Time (JIT) Production
Just-In-Time production aims to reduce flow times within the production system as well as response times from suppliers and to customers. It focuses on producing what is needed, when it’s needed, and in the amount needed, reducing waste and inventory costs.
- Dell leveraged JIT principles to revolutionize its manufacturing process, enabling the company to hold inventory for less than eight hours before it's turned into a finished product. This drastic reduction in inventory levels contributed to Dell's ability to offer lower prices and faster delivery times than its competitors.
Enhancing Best Practices with Avatour
Integrating Avatour into your lean manufacturing strategy amplifies the effectiveness of these best practices. With its innovative 360° capture and collaboration technology, Avatour brings a new dimension to lean practices like Gemba walks and Kaizen meetings. It allows teams to engage in real-time, immersive collaboration, making it easier to identify improvement opportunities, regardless of physical location.
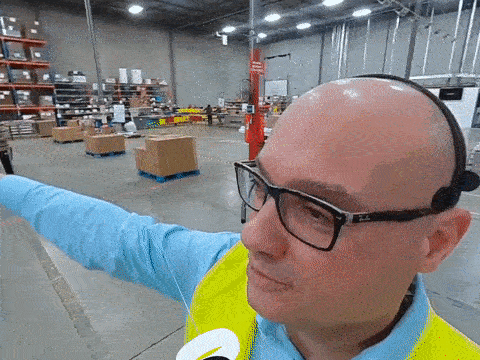
By breaking down geographical barriers, Avatour ensures that the principles of lean manufacturing can be applied more broadly and effectively, enabling companies to achieve operational excellence with greater speed and less waste. Whether it's improving 5S compliance through virtual audits or streamlining value stream mapping processes across global facilities, Avatour offers a suite of benefits that enhance lean manufacturing initiatives.
Lean manufacturing is a journey of continuous improvement and operational refinement. With these best practices and the support of technologies like Avatour, companies can navigate the complexities of modern manufacturing, driving efficiency, reducing waste, and ultimately delivering greater value to their customers. Explore Lean Manufacturing Tools, Lean Manufacturing Benefits, and insights on How to Implement Lean Manufacturing for a deeper dive into maximizing your lean manufacturing potential. Together, let's build a future where lean principles and innovative technologies like Avatour drive industry forward.