The Lean practice of a Gemba Walk is a powerful way to enhance operational efficiency through first-hand observation and direct interaction with the workers performing the tasks. By closely examining workflows, processes, and worker experiences, continuous improvement professionals can identify inefficiencies and develop effective solutions. However, Gemba Walks involve more than just walking through a site; they require careful planning and execution to make a real impact. Here’s a detailed guide to help you maximize the benefits of your next Gemba Walk.
Let’s take a look at our 10 essential tips:
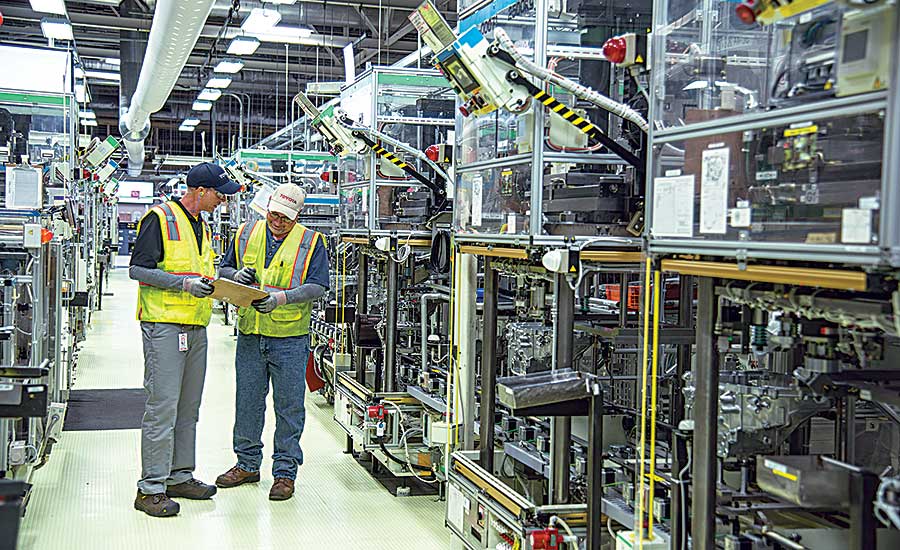
Ten Essential Tips for a Successful Gemba Walk
1. Prepare a Detailed Agenda
Before setting foot on the Gemba, outline the objectives and scope of the walk. This includes determining who will participate, planning the route, and defining the expected outcomes. Make sure to gather any relevant information, such as diagrams, maps, or data points, to aid the team during the walk. Address any safety precautions necessary for the specific environment.
Avatour Tip: If physical presence is a challenge, consider leveraging Avatour's remote collaboration capabilities. The platform allows team members to participate in Gemba Walks from anywhere using real-time 360° video technology, enabling seamless remote observation and engagement.
2. Gather the Right Team
The success of a Gemba Walk depends heavily on involving the right people. Ensure you have team members with diverse expertise related to the process being observed. This helps in gaining a comprehensive understanding and facilitates the identification of improvement areas. Define each participant's role and responsibilities in advance, and provide any required training.
Bonus Tip: When it’s difficult for key stakeholders to be physically present due to travel constraints or time zones, Avatour’s technology offers a practical solution. With its remote collaboration technology well-suited for Gemba walks, team members can join the Gemba Walk remotely, providing valuable input without needing to be on-site.
3. Ask Insightful Questions
To gain deeper insights into the processes and identify areas for improvement, ask open-ended questions about the workflow, inputs, outputs, and worker experiences. Avoid yes-or-no questions to encourage detailed responses. Get the whole team involved in the discussion to foster a culture of continuous improvement.
4. Take Notes and Capture Visuals
Documenting observations is key to analyzing the process effectively later. Write detailed notes and use visuals to support your findings. Videos and photos are excellent for capturing intricate details that may not be immediately apparent.
Pro Tip: Utilize Avatour's 360° video recording features during virtual Gemba Walks to create a comprehensive visual log of the site. This provides an all-encompassing view that helps in recalling observations and supports data-driven decision-making during the follow-up phase. Learn how 360° cameras work.
5. Focus on root cause analysis
Don’t get caught up in the outcomes; identify the root cause of any problems or issues that arise. This is key in order to properly address the issue and ensure it doesn’t resurface.
Bonus Tip: When analyzing an issue, ask, “Why” at least 5 times in order to get from obvious symptoms to the root cause. Learn more about the 5 Whys practice from Lean Methodology.
6. Identify Potential Solutions
Brainstorm with the on-site experts to identify potential solutions. Engage workers who are directly involved in the process, as they often provide valuable insights that might not be visible from a managerial perspective. Focus on generating several options rather than finding the perfect solution immediately.
7. Communicate Findings
After the Gemba Walk, share your observations and suggestions with all relevant stakeholders. Transparency ensures everyone is on the same page regarding necessary changes and action plans.
Avatour Advantage: The platform allows you to record the entire Gemba Walk session, including real-time discussions. This feature is particularly useful for sharing findings and solutions with team members who couldn’t participate in the live session.
8. Prioritize Actions
Determine which solutions should be implemented first. Focusing on the highest-impact changes will maximize the efficiency of your improvement efforts. Be mindful of resource allocation to ensure the most critical issues are addressed promptly.
9. Follow Up to Ensure Effective Implementation
Tracking the progress of implemented changes is crucial. Schedule follow-up sessions to gauge the impact and make adjustments if necessary. Gather feedback from workers on the ground to refine solutions.
Avatour Enhancement: Conduct remote follow-up Gemba Walks with Avatour to monitor changes without requiring another physical visit. This can help you ensure continuous improvement while minimizing travel costs.
10. Celebrate Success
Recognizing accomplishments motivates your team and encourages a culture of continuous improvement. Highlight positive changes resulting from the Gemba Walk and celebrate the team’s efforts to implement these solutions.
The Future of Gemba Walks
The traditional Gemba Walk remains an invaluable tool for continuous improvement, but advances in technology have made it even more accessible and efficient. With platforms like Avatour, companies can conduct Gemba Walks virtually, offering remote and hybrid access to multiple sites without the need for travel. Avatour’s real-time 360° video technology replicates the experience of being on-site, enabling stakeholders to observe, interact, and collaborate just as they would during a traditional Gemba Walk.
By integrating Avatour into your continuous improvement strategy, you can:
- Reduce travel costs and time: Participate in Gemba Walks across different locations without the need for physical travel.
- Enhance collaboration: Involve global experts in real-time, allowing for diverse perspectives and quicker identification of root causes.
- Improve documentation and analysis: Record 360° walkthroughs for future reference and better-informed decision-making.
Learn the Pros and Cons of In-Person vs Virtual Gemba Walks and see which method is right for you and your team.
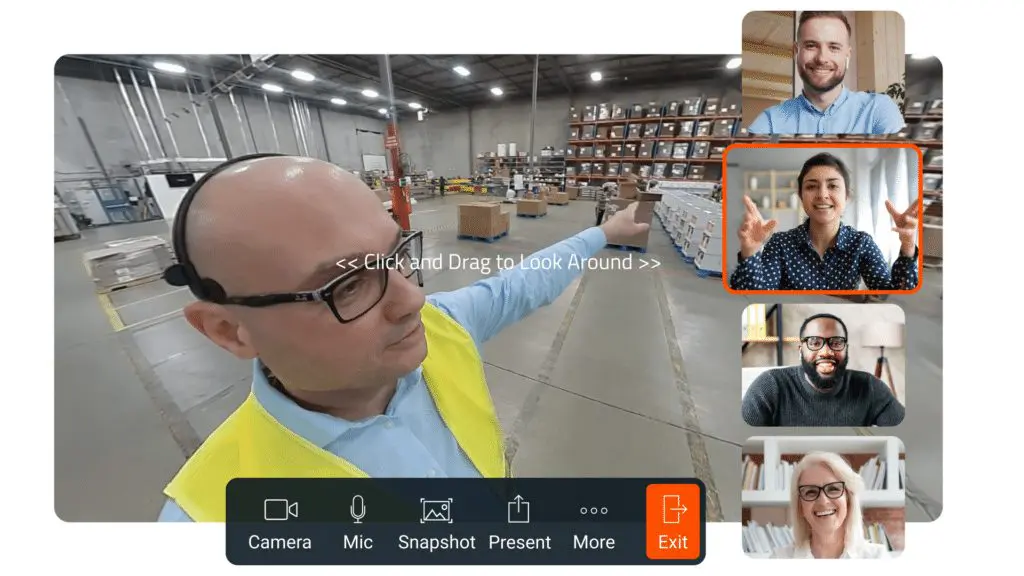
Avatour delivers the most effective way to walk the Gemba virtually.
With tools like Avatour, virtual Gemba Walks are no longer a concept of the future; they are a practical and effective option today. Whether managing a single site or multiple global locations, Avatour's platform ensures in-person visibility and collaboration without the hassles of travel. Incorporating this technology into your Gemba Walk checklist will not only streamline the process but also open up new possibilities for continuous improvement.
Click to learn more about the Avatour platform.