In the world of manufacturing, standing still is akin to moving backward. The drive for continuous improvement in manufacturing isn't just about keeping pace; it's about setting the pace, pushing boundaries, and finding new ways to solve old problems. But what does this look like in the face of today's manufacturing challenges? Let's dig in.
Tackling Modern Manufacturing Challenges Head-On
Manufacturing isn't what it used to be. The sector has evolved, becoming a complex beast that demands both agility and precision. Here are a few hurdles that modern manufacturers face:
- Supply Chain Complexity: Global supply chains are a marvel of modern commerce, but they're also fragile. A single disruption can ripple through the system, causing delays and shortages. Continuous improvement methods help by streamlining processes and finding redundancies that can be eliminated, making the whole chain more resilient.
- Quality Control Across Borders: When your manufacturing footprint spans continents, maintaining consistent quality becomes a Herculean task. Through continuous improvement, companies implement standardized processes and regular quality checks, ensuring products meet the same high standards, no matter where they're made.
- Rapid Technological Change: Technology advances at breakneck speed, and what was cutting-edge yesterday is obsolete today. Continuous improvement isn't just about keeping up; it's about staying ahead, integrating new technologies to improve efficiency and output.
- Sustainability Pressures: Consumers and governments alike are demanding more environmentally friendly manufacturing practices. This means finding ways to reduce waste, conserve energy, and minimize the carbon footprint. Continuous improvement methodologies are key to identifying and implementing these changes systematically.
- Labor Shortages and Skills Gaps: As experienced workers retire and technology evolves, the manufacturing sector faces a skills gap. Training and development, core components of continuous improvement, are vital in addressing this gap, ensuring workers are skilled in the latest technologies and methodologies.
Continuous Improvement in Manufacturing Operations: The Key to Unlocking Potential
So, how does continuous improvement help tackle these challenges? It's all about making small, incremental changes that add up to big impacts. By continuously assessing and optimizing processes, manufacturers can become more agile, better equipped to deal with supply chain disruptions, maintain quality across borders, integrate new technologies, reduce environmental impact, and bridge the skills gap.
Enter continuous improvement tools like Avatour, which offer a fresh perspective on traditional problems. With its 360° video capture and collaboration capabilities, Avatour lets teams dive into the heart of manufacturing operations, regardless of physical location. This means problems can be spotted and addressed faster, training can be conducted remotely, and best practices can be shared more easily across sites.
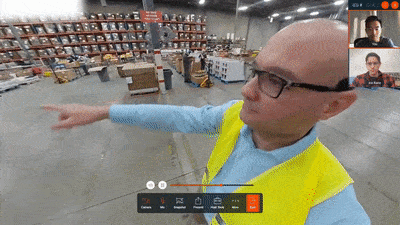
Continuous Improvement in Manufacturing -Challenges and Solutions
- Supply Chain Resilience: Continuous improvement efforts might focus on identifying critical suppliers and developing alternative sources, reducing reliance on a single supplier or region. Techniques like value stream mapping can help visualize supply chains, identify bottlenecks, and streamline processes for greater efficiency.
- Quality Assurance: Lean manufacturing principles, part of the continuous improvement philosophy, emphasize standard work and error-proofing to maintain quality standards. Regular kaizen events bring teams together to solve quality issues and implement solutions quickly.
- Embracing Tech Advances: Staying ahead technologically requires a culture of continuous learning and experimentation. For instance, using predictive analytics for maintenance can drastically reduce downtime, and 3D printing for prototyping can speed up the development cycle.
- Sustainability as a Core Value: Environmental improvements can also lead to cost savings. Energy-efficient machinery, waste recycling programs, and water conservation efforts not only help the planet but also improve the bottom line. Continuous improvement teams can lead the charge in identifying and implementing these initiatives.
- Overcoming the Skills Gap: Cross-training employees, creating comprehensive onboarding processes, and leveraging technology for remote learning are all continuous improvement strategies that address labor challenges. Tools like Avatour can facilitate remote, hands-on training, allowing new employees to learn directly from experts without the need for travel.
Moving Ahead
In the fast-evolving landscape of manufacturing, the principles of continuous improvement serve as a beacon, guiding companies through the challenges of modern production. While the hurdles are many, the discipline of continuous improvement offers a structured approach to navigating them, fostering a culture of innovation, efficiency, and resilience.
As we look ahead, continuous improvement tools like Avatour are proving to be invaluable allies in this journey. By enabling real-time collaboration and visibility, they break down barriers of distance and time, allowing teams to work together more effectively than ever before. It's not just about solving today's problems but building the foundation for tomorrow's success.
Whether it's streamlining your supply chain, elevating quality control, integrating the latest tech, going green, or closing the skills gap, continuous improvement is the key. And with the right tools and a committed team, there's no limit to what can be achieved.